Mikimoto Ginza 4-Chome Store
Rippling waves sparkle in the middle of Ginza [Part 1]
Design: Hiroshi Naito, KAJIMA DESIGN
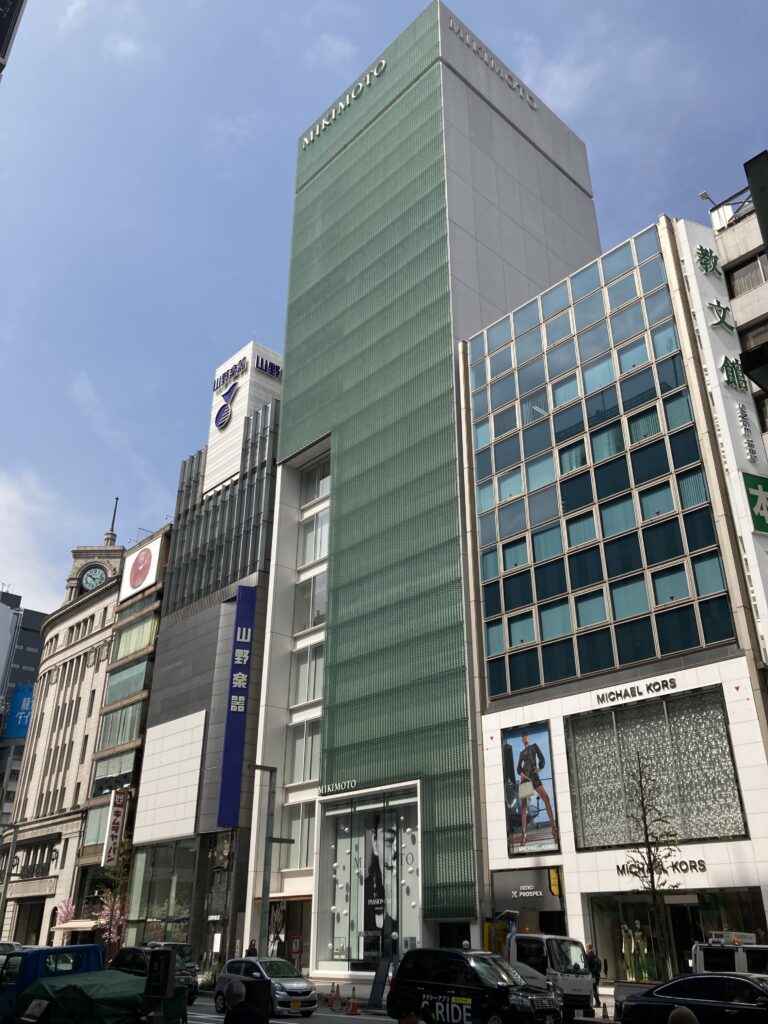
About me
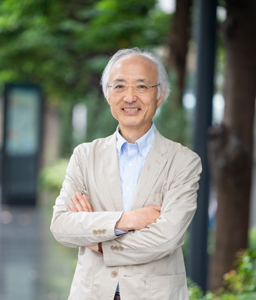
Yasuo Nakamaru
Registered Architect and National Government Licensed Guide Interpreter.
Worked at an architectural firm for 38years and designed domestic works and overseas works in Japan, US, UK, China, etc.
Favorite Buildings: National Gallary of East Wing by I.M.Pei in the US, Kimbell Art Museum by L.Kahn in the US, 21st Century Museum of Contemporary Art by SANAA in Japan
Favorite Things: Playing bass guitar, Jazz Music
日本語記事はこちら
On the main street in Ginza, the image of the seascape of Toba appears on the wall twice a day, morning and evening.
In this part, we are going to focus on how this image was created, and learn about the enormous and meticulous design work and craftsmanship that made it possible to realize the project.
In addition, we will explore what was happening inside the temporary enclosures during construction.
Image Realization Process
The Mikimoto Ginza Main Store, designed by Hiroshi Naito, is one of my favorite buildings in Ginza.
Every time I pass by this building, I stop there and look up.
The composition of its facade is the only one of its kind in Ginza. The more I learn about the details of its composition, the more I sense the deep consideration for the ideas and examination process that brought the image to life, and the craftsmanship that supported it.
What was Naito’s inspiration for designing the facade of Mikimoto’s main store?
It was the seascape of Toba, Mie Prefecture, and the rippling waves shining in the sun.
Toba is the birthplace of Mikimoto.
Naito chose the ripples on the sea in Toba as an image of the Mikimoto building, and aimed to reproduce them on its wall surface.
Twice a day, in the morning and evening, the ripples of Toba sea appear on the wall surface, which turns into the sea.
The reflected light comes inside the building and appear on the ceiling.
The sea of Toba was always a source of encouragement to Naito when he visited the site to work on his first recognized work, Toba Sea-Folk Museum.
To express his sentiment and memory, he created a facade composed of 38,000 pieces of glass.
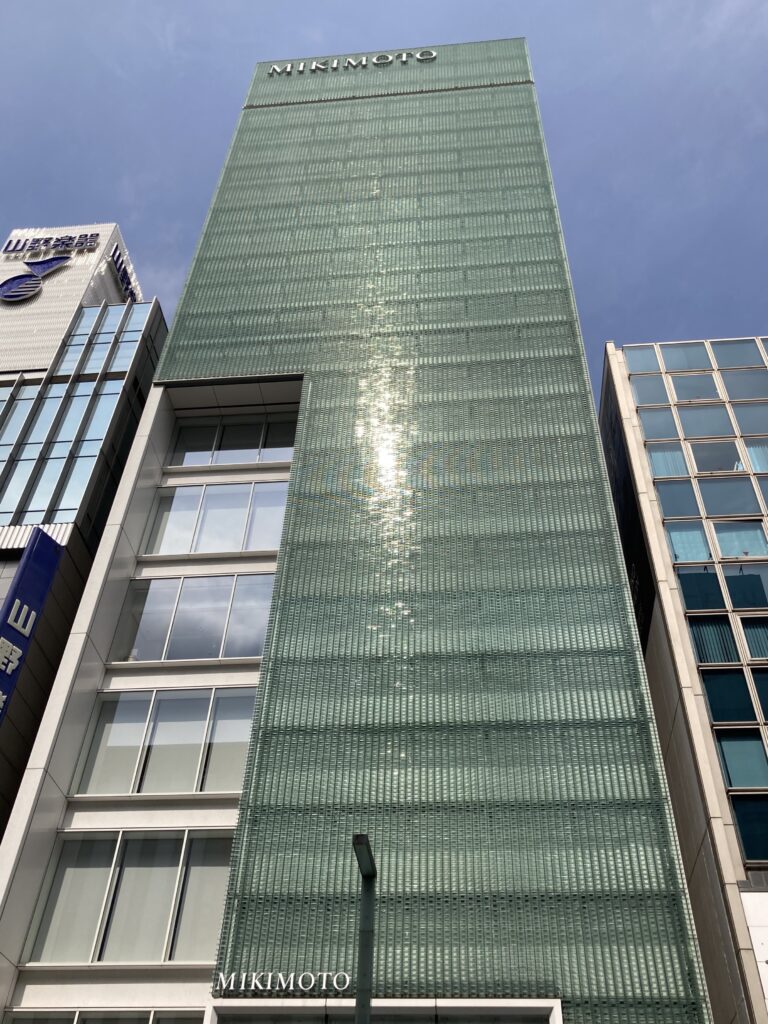
How did he create the image of the sparkling sea?
Glass was chosen as the material, and then Naito and his team started to examine a variety of options, including glass selection, processing methods, and fabrication methods.
There are various types of glass. They selected float glass for this project from among high-transmission glass, fused glass, and optical glass. Dozens of pieces were tested for strength checks.
The size of one piece of glass is 70mm wide, 280mm long, and 21mm thick. Glass-covered part of its façade is about 750 m2. That means there are about 50 pieces of glass installed in one meter square.
Must have taken so much time and effort to make so many glass pieces.
There is a photo of a young craftsman, on the Shinkenchiku, Japanese architectural magazine, manually installing the glass pieces into the unit at the factory. This is a fruit of such meticulous works.
Without being polished, the cut edges of the glass pieces are finished to reflect light like the surface of water. Also, that made the whole processing work more efficient.
The full-scale models and samples must have been checked in the production process. For ease of installation onsite, a unitized assembly method was adopted.
The glass surface is tilted 3 degrees inward to prevent water drops from overflowing to the outside, and 38,000 pieces of glass were assembled with high precision. The diligence and enthusiasm of the craftsmen who conducted the installation were brought together to create this unique façade in Ginza.
For Creation of High-Quality Architecture
Naito’s works are known for high quality and refinement. What does he do to create such works?
The construction drawings by architects are the basis for construction as a means of communicating a well-developed plan to contractor.
However, according to Naito, there is a limit to what can be expressed in a two-dimensional drawing for a three-dimensional building.
It is surprising to learn that even for Naito only 40% of the idea can be expressed on blueprints. Then, how can the remaining 60% be expressed?
In fact, it is not the case that the architects’ role is finished once the drawings are done and contractor does the rest.
The works continue inside the temporary enclosures during the construction.
During the construction phase, additional details, reviews, and revisions are being made to further fill in the remaining 60%.
The construction phase is the process of final confirmation and realization of what architects plan to express.
Also, during this period, various constraints such as cost, time, and weather must be taken into consideration.
On the other hand, the builders do not simply follow the drawings. And if it is the work of a major architect, the construction company naturally put so much effort into the project.
A former atelier designer once told me that when he supervised on construction site, he must be ready to redo the design all over again if necessary.
The impression of finished building will be completely different depending on the supervision. That is the reason why construction phase is so important.
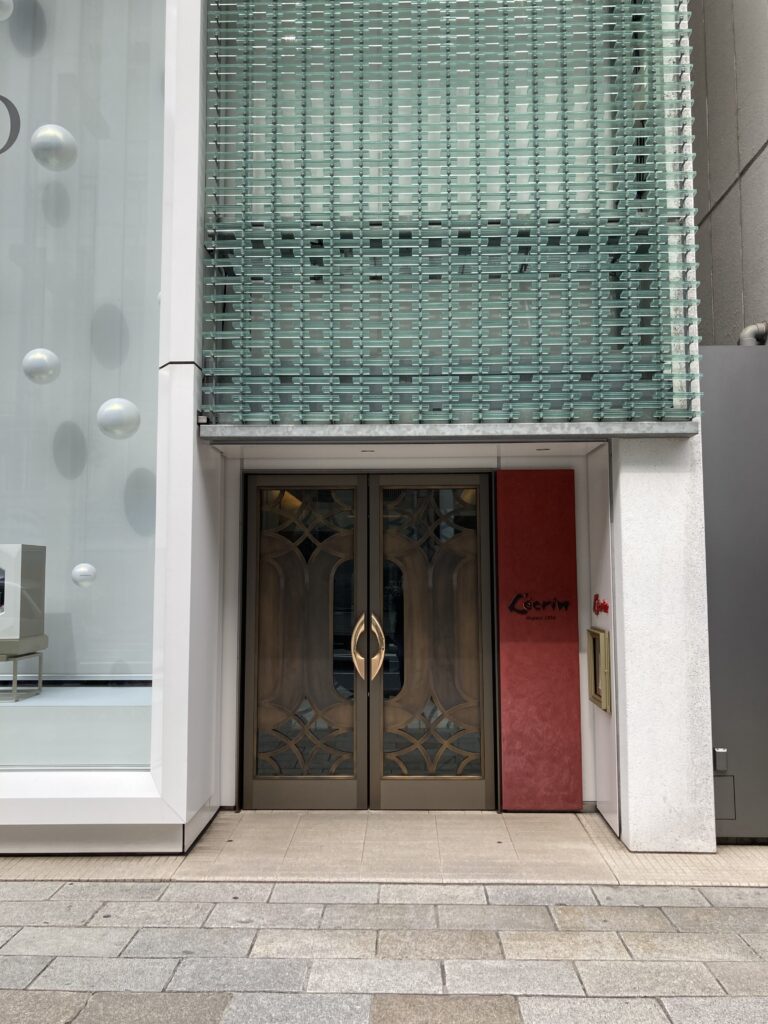
Important tasks during on-site construction
What is being done on site?
More examinations are waiting to be done, such as detailed studies of areas not fully expressed in design drawings, proposals from construction side, production problems, selection of color, performance, finish selection, and so on.
For construction site, working drawings are made by contractor for workmen based on architects’ drawings.
In this part, more problems and options for the actual construction are discussed.
For exposed-concrete building, formwork is allocated in millimeters, and position of plastic cones is determined.
Since drawings for foundation work include piles, footings, reinforcing bars, etc., number of drawings is more than 10 or 20 times of the original drawings by design office. Workmen on each construction project conduct actual construction based on these drawings.
All fabrication items, such as built-in furniture or custom-made hardware, also require drawings.
For the façade of Mikimoto Ginza, the fabrication and installation method of the exterior glass pieces must have been carefully considered, not only for their strength but also for workability and on-site installation.
At this stage, adjustments in construction and fabrication, problem solving, further detailing, maintainability, and workability under the restrictions on the Ginza site are considered.
Mockups (full-scale samples) are used to further examine color, workability, and other aspects of the building to be upgraded.
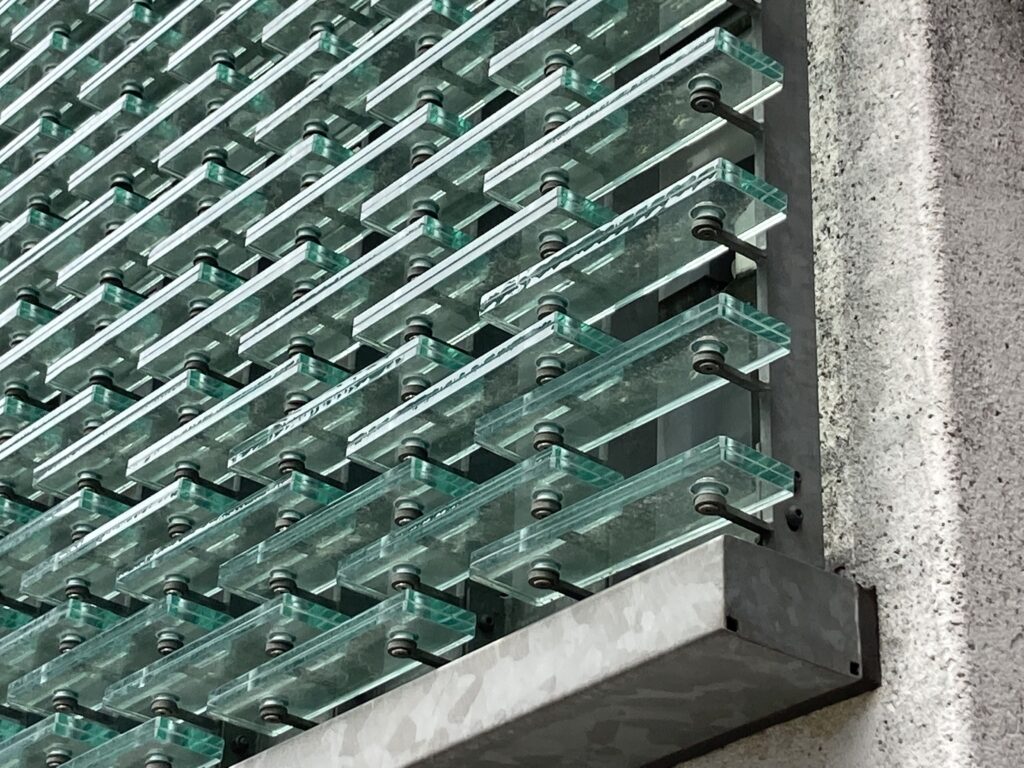
If examination at this stage is not thorough enough, or if they do not take enough time to further refine the work, it may end up with a building that is not as good as it should be.
For architects, building process is like creating a full-scale model, and it is a place where the expected and the unexpected happen.
I am wondering how much of Naito’s ideas could be expressed in the finished form of this building, after going through so many considerations.
In his book, Naito says that his previous works score only about 60 points out of 100.
I was surprised to learn that even an architect like Naito is that strict with his works, and at the same time, I was touched by the depth of design work, endless studies, and architects’ thoughtfulness.
This is the reason why I always stop in front of this building and imagine these things.
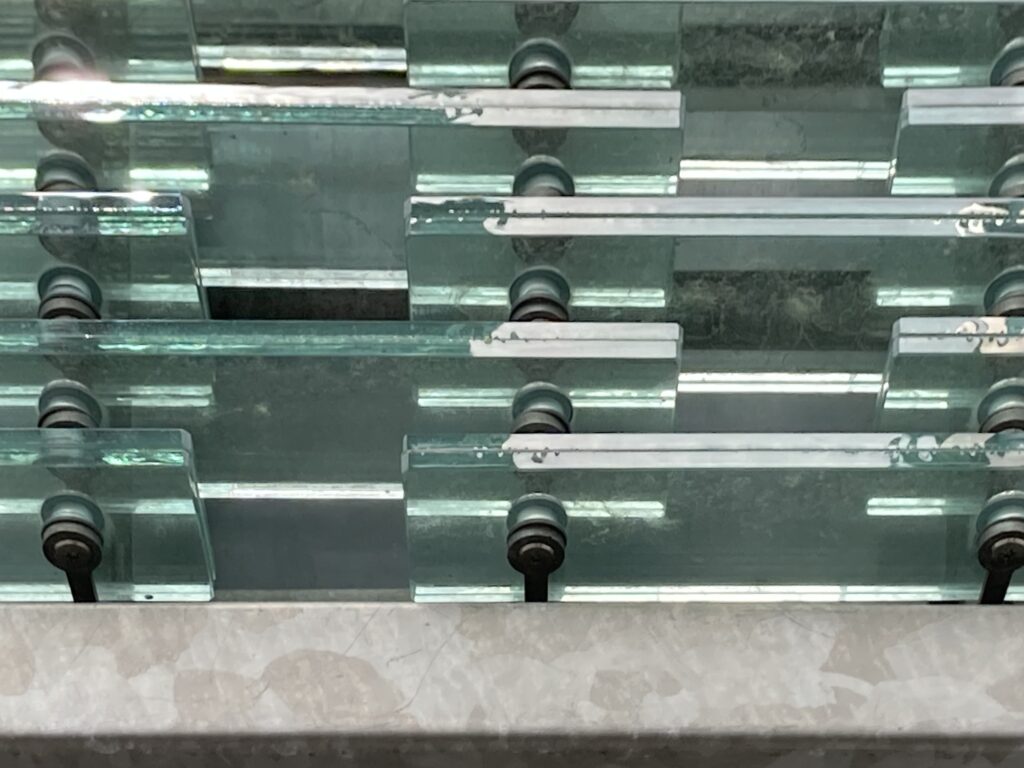
God of Design
Naito’s another notable work is The Shimane Arts Center (2005). For this building, Naito created a total of 1,400 drawings. How many detail drawings were drawn for the entire construction, then? It must have been a struggle with the drawings. Naito says that his memory was at its limit.
The same materials are used repeatedly to create a unique architectural beauty. The use of roof tiles for its walls added an unexpected effect. The earth-colored tiles turn blue or red in accordance with the weather.
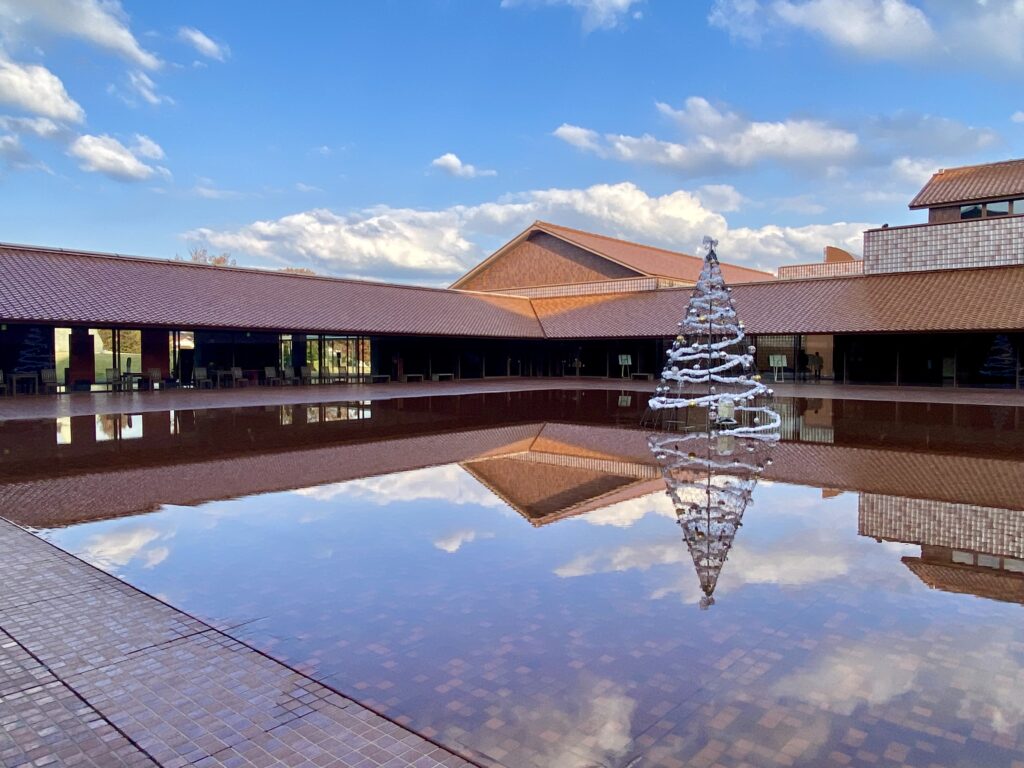
The use of “Sekishu” tiles, a roofing material, for the walls also gave different looks that the architect had not imagined. The tile craftsmen were the most surprised. This is truly an architect’s dream come true.
Naito once said that the God of architecture gives a reward if architect works diligently on each project with careful consideration. Naito’s words make my heart filled with excitement as I imagine the severity of the design work and the sense of accomplishment when the project is completed.
To be continued in the next article…
Mikimoto Ginza 4-Chome Main Store
〒104-0061
5-5, 4 chome Ginza, Chuo-ku, Tokyo